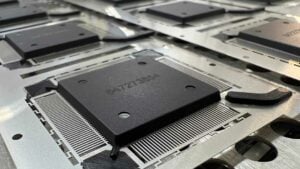
Material | Tmax (C°) | X-Y CTE (ppm) | Thermal Conductivity (W m-1 K-1) | Electrical Conductivity (106 S m-1) | Dk | Df |
---|---|---|---|---|---|---|
FR-4 | 125 | 10-14 | 0.3-0.9 | < 1E – 20 | 3.9 – 4.5 | 0.02 |
BT – Epoxy | 210 | 10-14 | 0.7 | < 1E – 13 | 3.6 – 3.7 | 0.01 |
Polyimide | 250 | 6-9 | 0.7 | <5E – 20 | 3.6 | 0.002 |
ABF | 150 | 20-40 | 0.15 | unknown | 3.2 – 3.4 | 0.004 – 0.02 |
Silicon | 2500 | 2.6 | 130 | 1 – 100 | 11.7 | 0.0005 – 5 |
Borosilicate Glass | 755 | 3.2 | 1.1 | 1E – 8 | 4.1 | 0.004 |
Copper | 2000 | 16 | 400 | 59 | – | – |
Gold | 1100 | 14 | 310 | 41 | – | – |
Silver | 960 | 20 | 429 | 63 | – | – |
Nickel | 1500 | 13 | 97 | 14 | – | – |
SN63/Pb37 | 170 | 25 | 40 | 7 | – | – |
SAC3005 | 210 | 24 | 58 | 9 | – | – |
Sn10Pb90 | 260 | 28 | 36 | 5 | – | – |
Custom tooling is designed and fabricated in house. ISI has a complete tool & die shop with decades of mold tooling fabrication expertise.
Ultra-dense, SWaP-optimized microelectronic assemblies.
Survive harsh environments;
Temperature cycle, shock, and vibration.
Integration of sensors with microelectronic modules.
Multi-component modules in standard IC form factor
(BGA, QFP, etc.).
Replace obsolete ICs with a form/fit/function equivalent module.
Your message will go to our in-house technical sales team. We typically get back within one business day.